Japan’s Winning Edge: Specialized “Genba AI”—Exploring Japan’s Future Through Manufacturing
2025.03.30
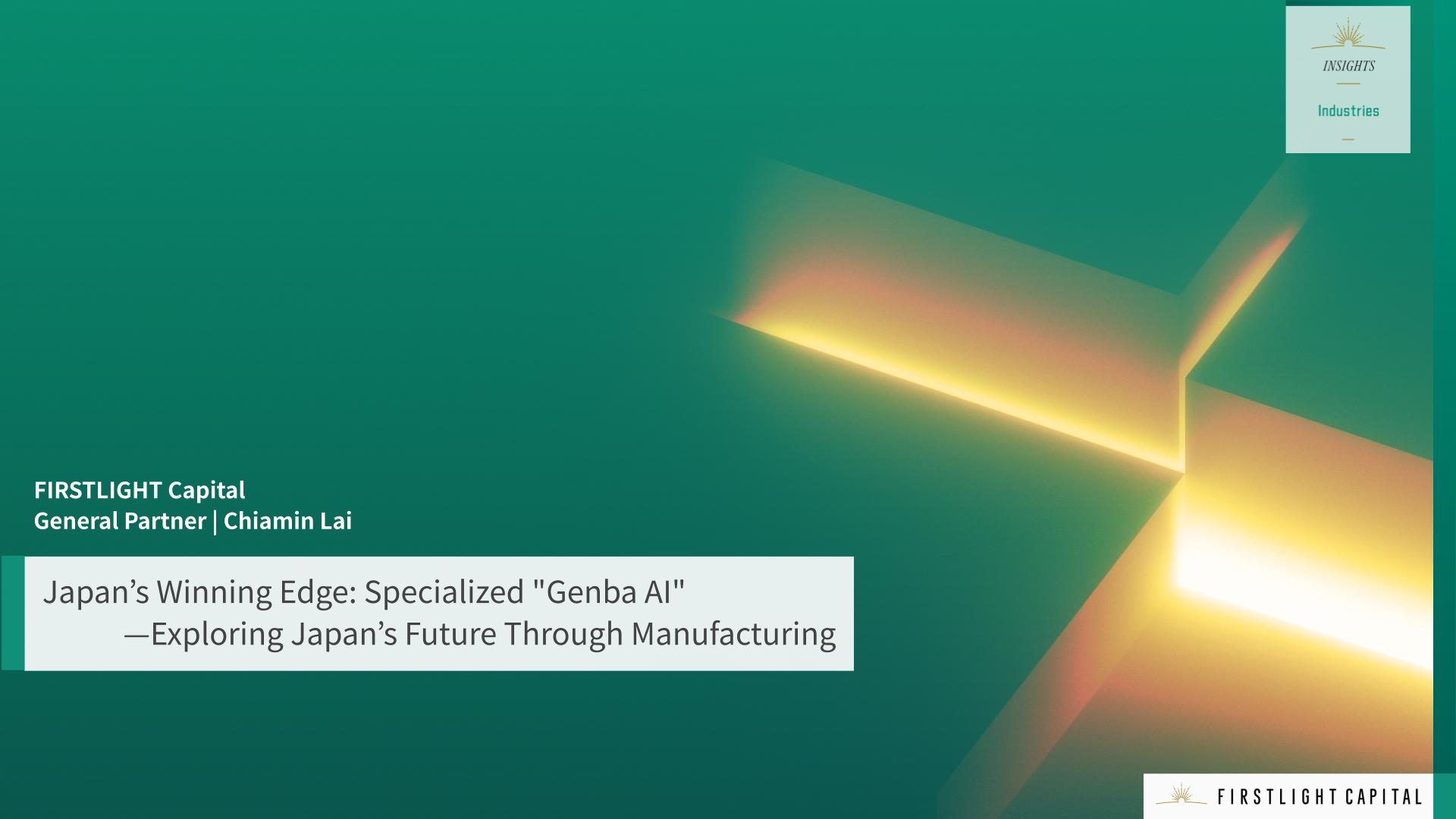
At FIRSTLIGH Capital, we’ve long focused on investing in SaaS companies and sharing key insights through resources like our SaaS Annual Report. Since 2021, however, we’ve expanded our focus beyond traditional SaaS to explore the convergence of hardware, SaaS, and AI.
Initially, the market paid little attention to this intersection of hardware and SaaS. However, we firmly believe that integrating AI into this nexus will bring genuine innovation to the “genba”, or “frontline” starting with Japan’s manufacturing industry and extending across other frontline sectors.
This isn’t about chasing the generative AI hype. It’s about capitalizing on one of Japan’s few realistic opportunities to establish a meaningful global presence in the AI space.
Silicon Valley startups raise massive funding rounds early and aim to scale globally from day one. In contrast, Japanese startups often focus on the domestic market and face structural hurdles in scaling internationally. To break through, Japanese startups must leverage a unique asset: deep-rooted expertise in complex industrial workflows, combined with an unmatched capability for on-the-ground adaptation and continuous improvement—what we call genba-ryoku, or “frontline excellence.”
Japanese companies are globally respected for their ability to deliver practical, high-precision solutions to real-world problems. This on-the-ground problem-solving strength, cultivated through decades of industrial experience, is an underutilized strategic advantage.
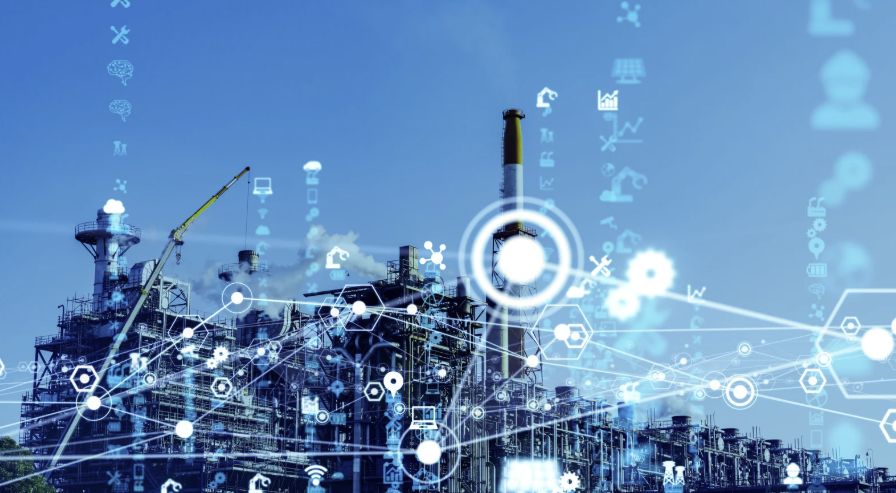
We believe Japan can establish a sustainable competitive edge by fusing this genba-ryoku with digital transformation (DX) in ways that are extremely difficult for Silicon Valley-born startups to replicate.
In this article, we explore the potential of AI in manufacturing and what it takes for Japan to lead globally in this arena
The Massive “Genba” DX Market is Entering a Phase of Accelerated Growth.
In recent years, while horizontal SaaS solutions have broadly penetrated the US market, specific industries like manufacturing, construction, and logistics remain underserved due to their unique workflows and entrenched business practices.
Consequently, vertical SaaS startups focusing on industry-specific solutions have emerged and achieved notable market positions.
In mature markets like the US, vertical SaaS solutions create value in four key areas:
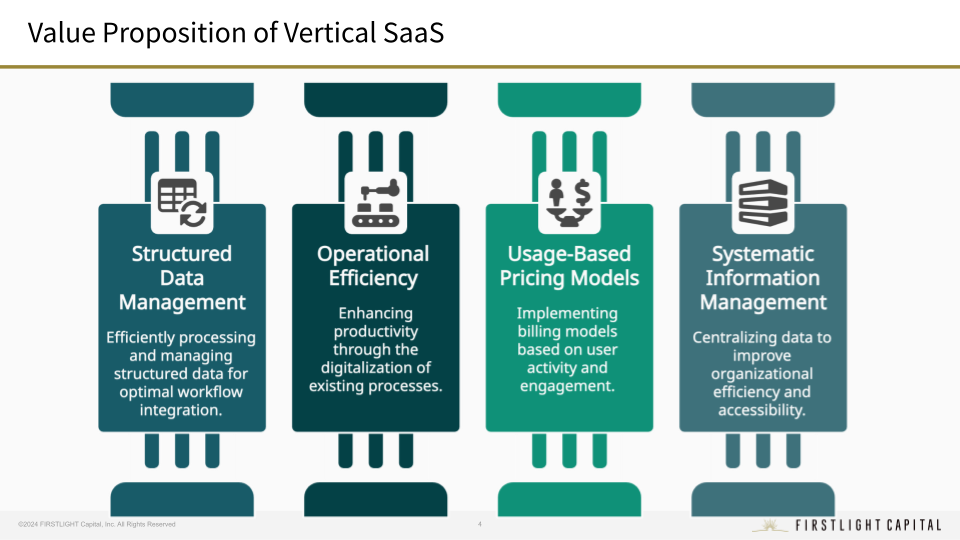
- Structured Data Management: Efficiently processing structured data suited to databases and workflows, such as customer information and inventory management.
- Operational Efficiency: Digitalizing existing processes to enhance productivity.
- Usage-Based Pricing Models: Introducing usage-based billing tailored to user numbers and activity.
- Systematic Information Management: Centralizing data through digitalized processes to boost organizational efficiency.
Japan’s vertical SaaS market is also gradually expanding, with significant growth anticipated particularly in manufacturing, construction, and logistics frontline DX sectors. Companies like CADDi (facilitating corporate DX through drawing data utilization) and ANDPAD (offering operational management services for the construction industry) exemplify successful vertical SaaS adoption in Japan.
Yet, promoting DX in these industries has challenges. Current vertical SaaS solutions primarily streamline back-office operations, leaving seamless frontline DX solutions still lacking. Complex workflows, entrenched industry practices, and extensive unstructured data like technical service records, quality assurance documents, supplier audits, production reports, and quality control imagery further complicate software-only DX initiatives.
Leveraging IoT and edge AI technologies for frontline data collection and smart operations is critical. Such technologies can significantly enhance vertical SaaS value and accelerate industrial DX. For instance, manufacturing environments increasingly utilize IoT sensors for real-time data acquisition and edge AI for quality inspections and anomaly predictions, adding significant value beyond operational efficiency alone.
In the U.S., companies integrating IoT hardware with vertical SaaS have experienced rapid growth, exemplified by Samsara, which went public in 2022. Samsara has achieved significant success by swiftly analyzing physical data collected from operational sites using AI to facilitate real-time decision-making.
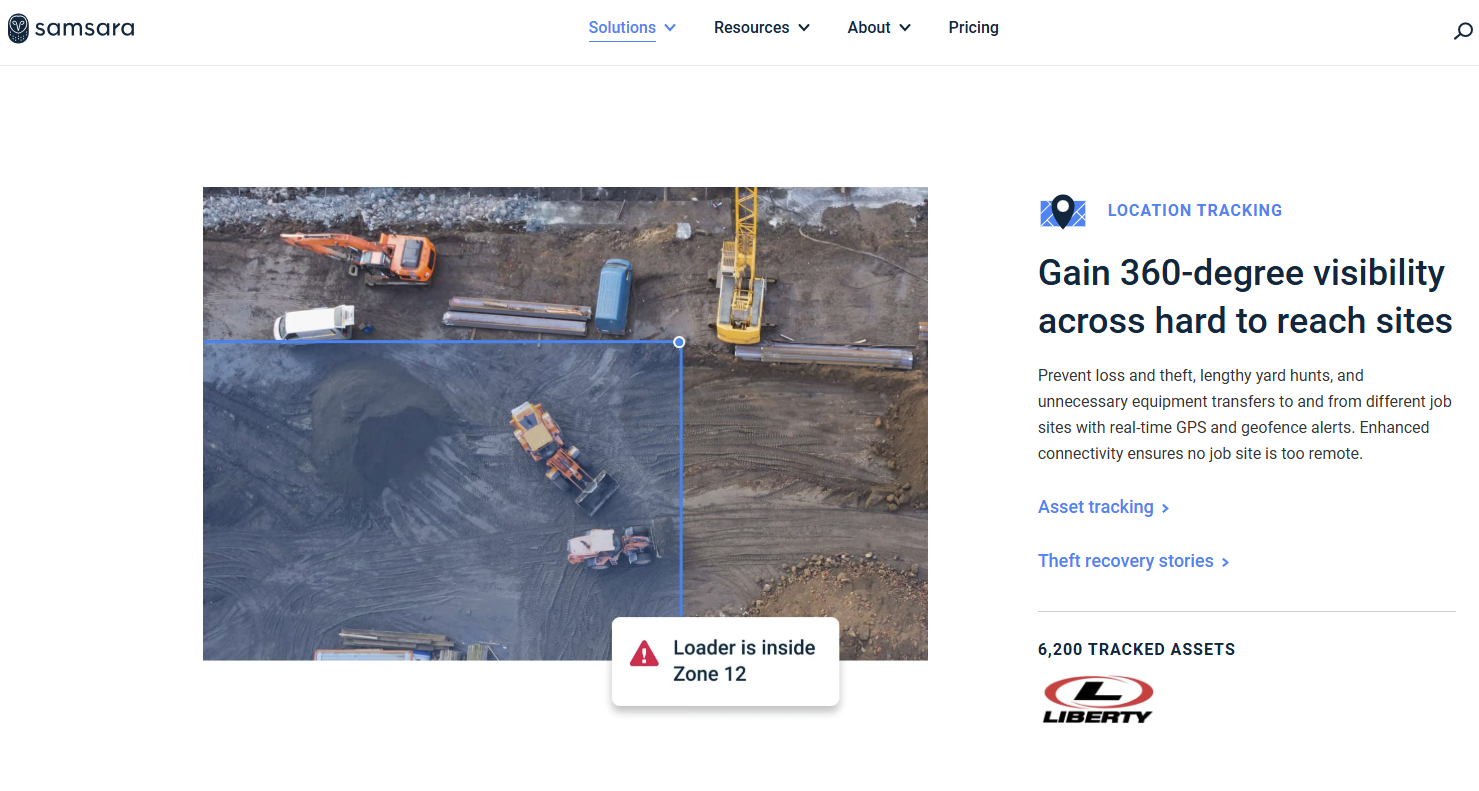
* HP of Samsara
Japan’s declining workforce and aging demographics have intensified the urgency of productivity improvements and operational efficiency, positioning DX and automation as critical infrastructure for sustainability.
Specifically, advanced generative AI solutions capable of real-time decision-making and process automation based on physical “genba data” are essential components for market growth.
Building AI Strength Through Japan’s Unique Industrial Structure
We identify four key reasons why Japan must prioritize the intersection of manufacturing and AI:
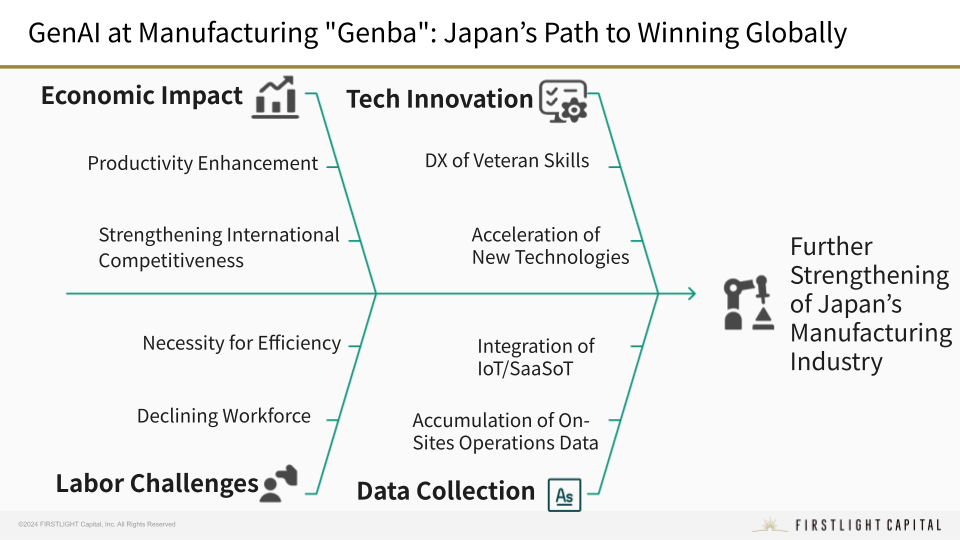
- Economic Impact and Industrial Scale:
Manufacturing contributes roughly 20% of Japan’s GDP, solidifying its status as an economic pillar. Innovations within this sector, notably through AI integration, promise not only heightened productivity but also the advancement of high-value product development, significantly boosting Japan’s global competitiveness. - Demographic Pressures:
Projections indicate a labor shortage of 11 million workers by 2040. Traditional sectors such as manufacturing, construction, and logistics are already experiencing acute labor shortages. Robotics alone is insufficient to fully compensate for this workforce gap, underscoring the urgent need for AI-driven process optimization. - From Skill Preservation to Technological Innovation:
Skilled labor shortages pose risks not only to productivity but also to the continuity of craftsmanship. AI solutions can digitalize and quantify nuanced human expertise previously reliant on intuition and tacit knowledge. This shift not only preserves essential skills but accelerates innovation by fundamentally transforming production processes. - Japan’s Manufacturing as a Data Goldmine:
Global leadership in generalized large-language models (LLMs) is dominated by the US and China, making competition in this saturated market challenging for Japan. Instead, Japan can differentiate by capitalizing on unique, high-quality data derived from its manufacturing sector. The rich repository of tacit, multi-dimensional sensory data from skilled craftsmen—unavailable online—represents an unparalleled resource for competitive advantage in specialized AI applications.
To effectively collect this data, companies must adopt an approach that incorporates IoT- and sensor-enabled operational SaaS solutions, simultaneously driving operational efficiency while accumulating essential data to power AI development.
The integration of IoT, sensors, and SaaS platforms is critical to systematically capturing valuable operational data.
Takumi Giken Industry, one of our portfolio companies, exemplifies this approach. Their specialized cost-estimation SaaS solution, “Takumi Force,” systematically aggregates multimodal data throughout component manufacturing processes, digitizing insights traditionally confined to seasoned craftsmen. By integrating standardized cost data and detailed technical drawings into comprehensive databases, Takumi Force significantly enhances pricing accuracy, operational profitability, and effective knowledge transfer. Moreover, leveraging this data through AI-powered decision-making tools further optimizes factory management and drives continuous innovation..
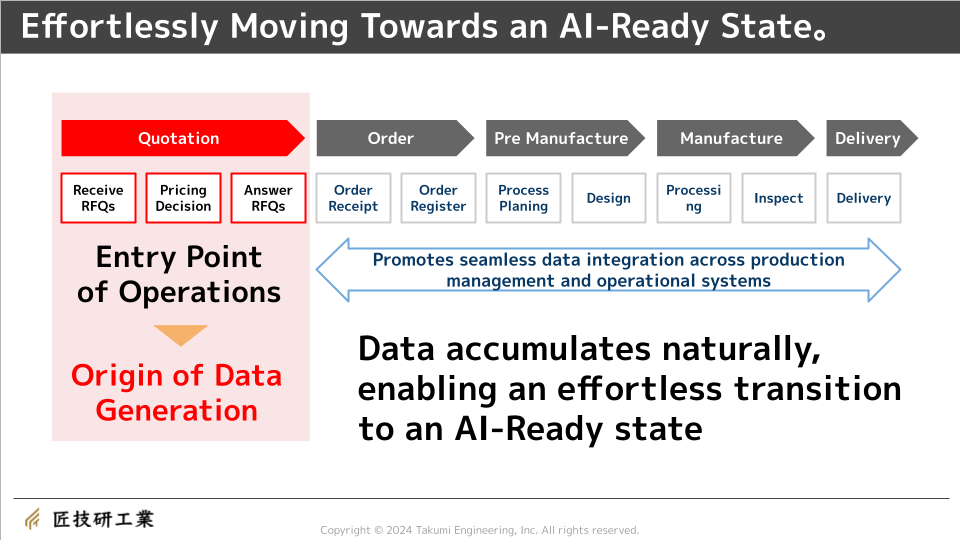
* From Takugi-ken Industries Co., Ltd. note
Through these initiatives, quantifying the intuitive skills of craftsmen significantly enhances productivity and precision in quality management. Additionally, AI models that support and augment decision-making by skilled artisans and management teams promise improvements in operational accuracy and creation of new value-added opportunities.
- Transform demographic challenges into advantages
- Leverage Japan’s established manufacturing strengths
- Rapidly digitize unique operational data exclusive to Japan’s industrial sites
The synergy of these factors can forge a robust “Manufacturing × Generative AI” ecosystem, presenting substantial growth opportunities for startups operating in this field.
Are Skilled Craftsmen the Ultimate Multi-modal Edge AI?
Traditionally, manufacturing DX focused on digitizing manual documentation and implementing SaaS to streamline operations. However, the critical decision-making processes on the production floor involve integrating multimodal sensory data—visual, auditory, thermal, and tactile—far beyond basic analytics.
Addressing the shortage of skilled artisans requires deploying integrated hardware-sensor systems combined with AI to simulate and implement these complex human decision-making processes. Such advancements will enhance knowledge transfer efficiency, boost productivity, and sustain competitive advantage.
The essence of manufacturing innovation goes beyond digitizing paperwork. Real transformation lies in integrating AI-driven decision-making processes that consider multiple factors such as machine performance, environmental conditions, and material characteristics.
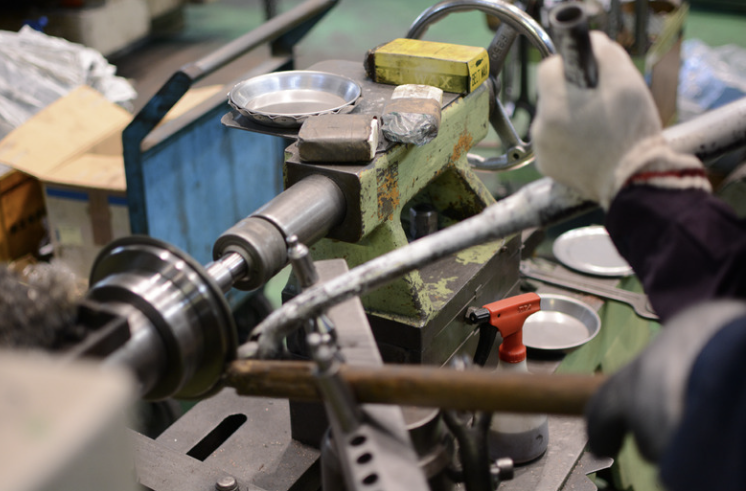
This complex, intuitive process can best be captured through multi-modal Edge AI solutions, combining visual, auditory, thermal, and tactile data streams to replicate human decision-making intricacies.
To successfully pass on this expert craftsmanship, it is essential to integrate hardware and sensor technologies in combination with AI.
By embedding sophisticated AI simulations within manufacturing workflows, enterprises can accelerate knowledge transfer, enhance decision-making accuracy, and significantly boost productivity.
Maintaining the Competitive Edge of Japanese Manufacturing Industries in the Future
Japan, historically renowned as a manufacturing powerhouse, faces declining global competitiveness due to delayed digitization and smart manufacturing implementations. While U.S. companies rapidly adopt advanced technologies like Copilot and AI agents, Japanese enterprises often remain stalled in proof-of-concept stages without scaling effectively.
Incremental AI adoption won’t be enough. What’s needed is a shift from localized tool usage to organization-wide optimization powered by AI. The winners of tomorrow will be those who fully integrate AI into core workflows.
In the AI era, competitive advantage depends on how quickly and effectively a company can collect, process, and operationalize data.
Japan’s manufacturing sector must accelerate its transformation. If done right, the combination of demographic urgency, industrial depth, and unique data can form the backbone of a globally competitive Manufacturing × AI ecosystem.
Now is the time to build it.
Written and by: Chiamin Lai | FIRSTLIGHT Capital General Partner
Edited by: Akio Hayafune | FIRSTLIGHT Capital Chief Analyst
Here at FIRSTLIGHT Capital, we regularly deliver useful content on both Japanese and global startup trends, as well as hands-on experience from our very own venture capitalists and specialists. Please feel free to contact us via the CONTACT page if you would like to be in touch. Click here to follow FIRSTLIGHT Capital’s SNS account!